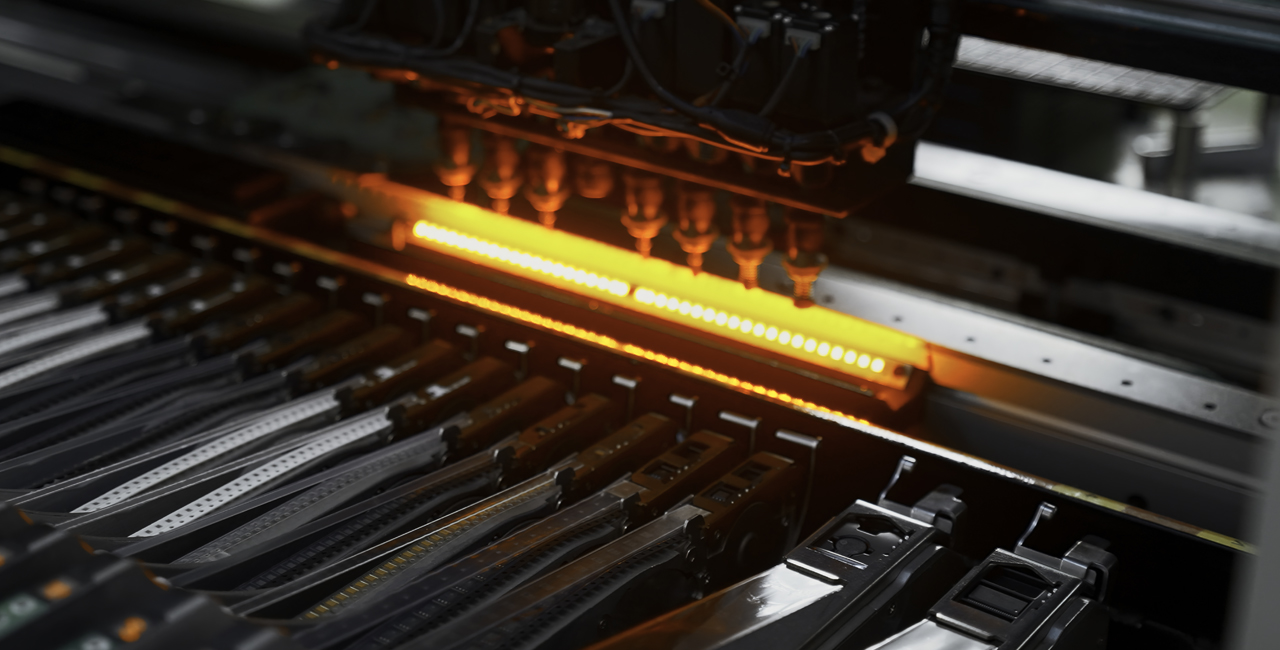
Surface Mount Technology (SMT) is a pivotal advancement in the realm of electronics manufacturing. It revolutionized the way electronic components are mounted onto printed circuit boards (PCBs). Unlike traditional through-hole technology, SMT allows for more compact and efficient designs, making it the go-to method for modern electronics production. This blog delves into the basics of SMT PCB assembly, exploring its process, advantages, and applications.
What is SMT PCB Assembly?
Surface Mount Technology (SMT) refers to the method of mounting electronic components directly onto the surface of a PCB. In contrast to through-hole technology, where components are inserted into drilled holes on the board, SMT components are placed on the board’s surface. This method utilizes surface-mount devices (SMDs), which are generally smaller and more efficient than their through-hole counterparts.
The SMT PCB Assembly Process
1. Solder Paste Application
The first step in SMT PCB assembly is the application of solder paste. Solder paste is a mixture of tiny solder balls and flux, which helps the solder to flow and adhere to the components. This paste is applied to the PCB using a stencil that aligns with the pads where the components will be placed.
2. Component Placement
Once the solder paste is applied, the PCB moves to the pick-and-place machine. This machine places the SMDs onto the board with high precision. The components are picked from reels or trays and accurately positioned on the solder paste.
3. Reflow Soldering
After component placement, the PCB undergoes reflow soldering. The board is passed through a reflow oven, where it is gradually heated to melt the solder paste. This process creates a strong mechanical and electrical connection between the components and the PCB. The oven has multiple temperature zones, ensuring controlled heating and cooling to avoid damaging sensitive components.
4. Inspection
Inspection is a crucial step to ensure the quality and reliability of the assembled PCB. Automated Optical Inspection (AOI) machines are commonly used to check for placement accuracy, solder quality, and defects such as solder bridges or missing components. X-ray inspection may also be used for more complex boards to verify hidden solder joints.
5. Testing
Functional testing is performed to verify that the PCB operates correctly. This may include in-circuit testing (ICT) to check individual components and connections, as well as system-level testing to ensure the board functions as intended in its final application.
Advantages of SMT PCB Assembly
1. Miniaturization
One of the most significant advantages of SMT is the ability to create smaller and more compact electronic devices. SMDs are generally smaller than through-hole components, allowing for denser and more efficient PCB layouts. This miniaturization is crucial for modern electronics, where space is often limited.
2. Higher Component Density
SMT allows for higher component density, meaning more components can be placed on a single PCB. This leads to increased functionality and performance without the need for larger boards. Higher density also translates to shorter electrical paths, improving signal integrity and reducing parasitic inductance and capacitance.
3. Automated Manufacturing
The SMT process is highly automated, which increases production speed and consistency while reducing labor costs. Automation minimizes human error, resulting in more reliable and higher-quality PCBs. This efficiency is particularly beneficial for large-scale production.
4. Improved Performance
SMT components often have better electrical performance compared to through-hole components. The shorter lead lengths reduce inductance, enhancing the performance of high-frequency circuits. Additionally, the improved thermal characteristics of SMT components contribute to better heat dissipation and overall reliability.
5. Cost-Effectiveness
Despite the initial investment in automated equipment, SMT can be cost-effective in the long run. The reduction in manual labor, increased production speed, and higher yield rates contribute to overall cost savings. Furthermore, the smaller size of SMT components can reduce material costs.
Applications of SMT PCB Assembly
SMT PCB assembly is widely used across various industries due to its versatility and efficiency. Some common applications include:
1. Consumer Electronics
Products such as smartphones, tablets, and laptops rely heavily on SMT for their compact and complex designs. The high component density and miniaturization enabled by SMT are essential for these devices.
2. Automotive Electronics
The automotive industry uses SMT in applications like engine control units, infotainment systems, and advanced driver-assistance systems (ADAS). The reliability and performance of SMT assemblies are crucial for automotive safety and functionality.
3. Telecommunications
SMT is used in telecommunications equipment such as routers, switches, and mobile base stations. The high-speed and high-frequency performance of SMT assemblies is vital for these applications.
4. Medical Devices
Medical devices, including diagnostic equipment, patient monitoring systems, and wearable health tech, benefit from the compactness and reliability of SMT assemblies. The precision and quality of SMT are critical in medical applications.
5. Industrial Automation
SMT is also prevalent in industrial automation and control systems. The robust and reliable nature of SMT assemblies makes them suitable for harsh industrial environments.
Conclusion
Surface Mount Technology has revolutionized the electronics manufacturing industry, offering numerous advantages in terms of miniaturization, performance, and cost-effectiveness. Understanding the SMT PCB assembly process and its benefits can help engineers and manufacturers make informed decisions to optimize their electronic designs. Whether in consumer electronics, automotive, telecommunications, medical devices, or industrial automation, SMT PCB assembly continues to drive innovation and efficiency in electronic manufacturing.