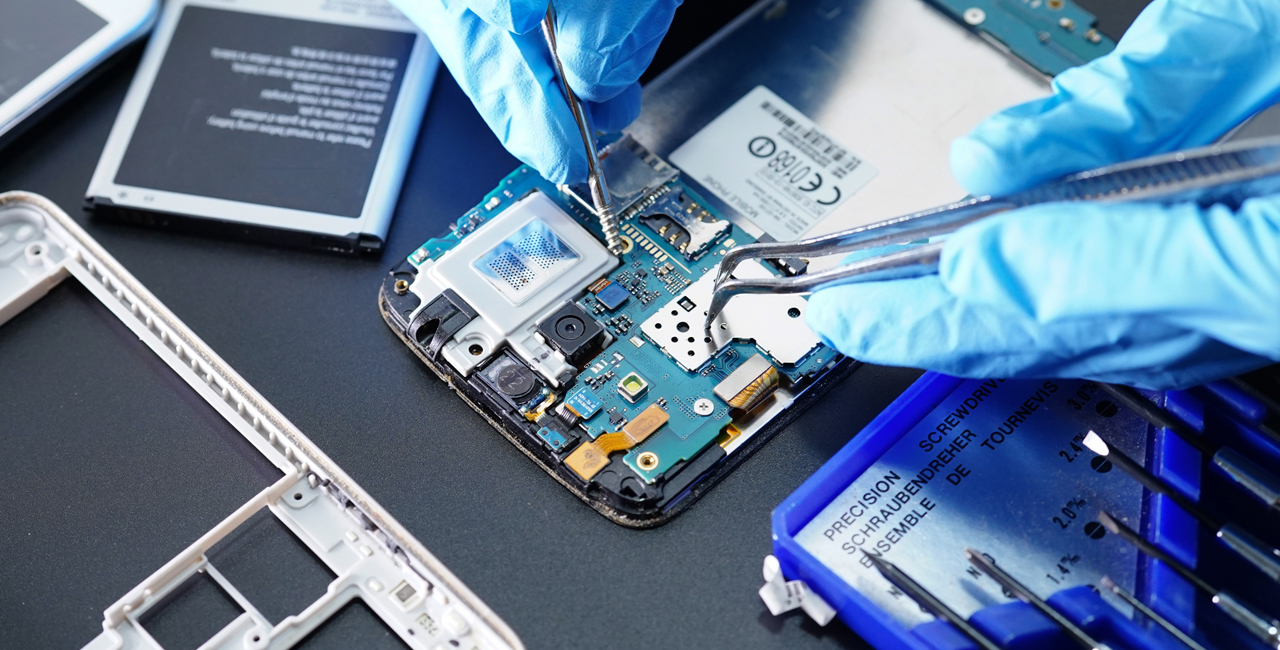
Printed Circuit Boards (PCBs) are the backbone of modern electronic devices, facilitating the interconnection of various components. However, as electronic devices become more powerful and compact, managing the heat generated by these components becomes increasingly critical. Effective heatsink design and selection are essential to ensure the reliability and performance of PCBs. This guide will delve into the fundamental aspects of PCB heatsink design and selection, providing you with the knowledge to make informed decisions.
Understanding the Need for Heatsinks
Electronic components generate heat during operation, and excessive heat can degrade performance, shorten lifespan, or even cause catastrophic failure. Heatsinks help dissipate this heat, maintaining the components within their safe operating temperatures. This is particularly important in high-power applications such as power supplies, amplifiers, and processors.
Key Factors in Heatsink Design
1. Thermal Conductivity
The primary function of a heatsink is to conduct heat away from the electronic components. Materials with high thermal conductivity, such as aluminum and copper, are commonly used. Aluminum is preferred for its balance between cost, weight, and thermal performance, while copper offers superior thermal conductivity but at a higher cost and weight.
2. Surface Area
The efficiency of a heatsink is directly related to its surface area. Increasing the surface area enhances heat dissipation by providing more space for the heat to transfer from the heatsink to the surrounding air. Fins and extended surfaces are commonly used to maximize the surface area.
3. Airflow
Effective airflow around the heatsink is crucial for heat dissipation. Natural convection relies on the natural movement of air, while forced convection uses fans or blowers to increase airflow. The design should consider the orientation and placement of fins to optimize airflow.
4. Size and Weight Constraints
The physical size and weight of the heatsink must be compatible with the PCB design and the overall device. Compact devices may require innovative heatsink designs to fit within limited spaces without compromising thermal performance.
Types of Heatsinks
1. Passive Heatsinks
Passive heatsinks rely on natural convection to dissipate heat. They are simple, reliable, and maintenance-free, making them suitable for low to moderate power applications. However, they may not be sufficient for high-power components without proper airflow design.
2. Active Heatsinks
Active heatsinks incorporate fans or blowers to enhance heat dissipation through forced convection. They provide superior cooling performance, making them ideal for high-power applications. However, they add complexity, noise, and potential points of failure due to moving parts.
3. Thermal Via and Heat Spreader
For multilayer PCBs, thermal vias can be used to transfer heat from the top layer to inner or bottom layers, where larger heatsinks or heat spreaders can be placed. Heat spreaders distribute heat across a larger area, improving overall thermal management.
Heatsink Selection Process
1. Determine Thermal Requirements
Identify the thermal requirements of your components by consulting datasheets and conducting thermal analysis. Determine the maximum allowable temperature and the power dissipation of each component to calculate the required thermal resistance of the heatsink.
2. Calculate Required Thermal Resistance
Thermal resistance is a measure of a heatsink’s ability to transfer heat. It is calculated using the formula:
θHS=Tmax−TambientPdissipated\theta_{HS} = \frac{T_{max} - T_{ambient}}{P_{dissipated}}
where θHS\theta_{HS} is the thermal resistance of the heatsink, TmaxT_{max} is the maximum allowable temperature, TambientT_{ambient} is the ambient temperature, and PdissipatedP_{dissipated} is the power dissipation.
3. Select the Appropriate Heatsink
Based on the calculated thermal resistance, select a heatsink that meets or exceeds this requirement. Consider factors such as material, size, weight, and cost. Use manufacturer datasheets and performance charts to compare options.
4. Optimize Placement and Mounting
The placement and mounting of the heatsink are crucial for effective thermal management. Ensure proper contact between the heatsink and the component using thermal interface materials (TIMs) such as thermal paste or pads. Optimize the orientation for natural or forced convection, and ensure adequate airflow around the heatsink.
Advanced Considerations
1. Thermal Simulation
Use thermal simulation software to model and analyze the thermal performance of your PCB and heatsink design. Simulation can identify potential hotspots and optimize heatsink placement and airflow design before physical prototyping.
2. Integration with PCB Design
Consider thermal management during the PCB design phase. Place high-power components strategically and use thermal vias, copper pours, and planes to improve heat spreading and dissipation.
Conclusion
Effective heatsink design and selection are vital for maintaining the performance and reliability of electronic devices. By understanding the key factors in heatsink design, selecting the appropriate type, and optimizing placement and mounting, you can ensure your PCBs operate within safe temperature limits. Advanced considerations such as thermal simulation and integration with PCB design further enhance thermal management, enabling the development of robust and high-performance electronic products.
By following this comprehensive guide, you can navigate the complexities of PCB heatsink design and selection, ensuring your electronic devices remain cool, reliable, and efficient.